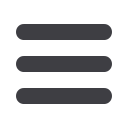
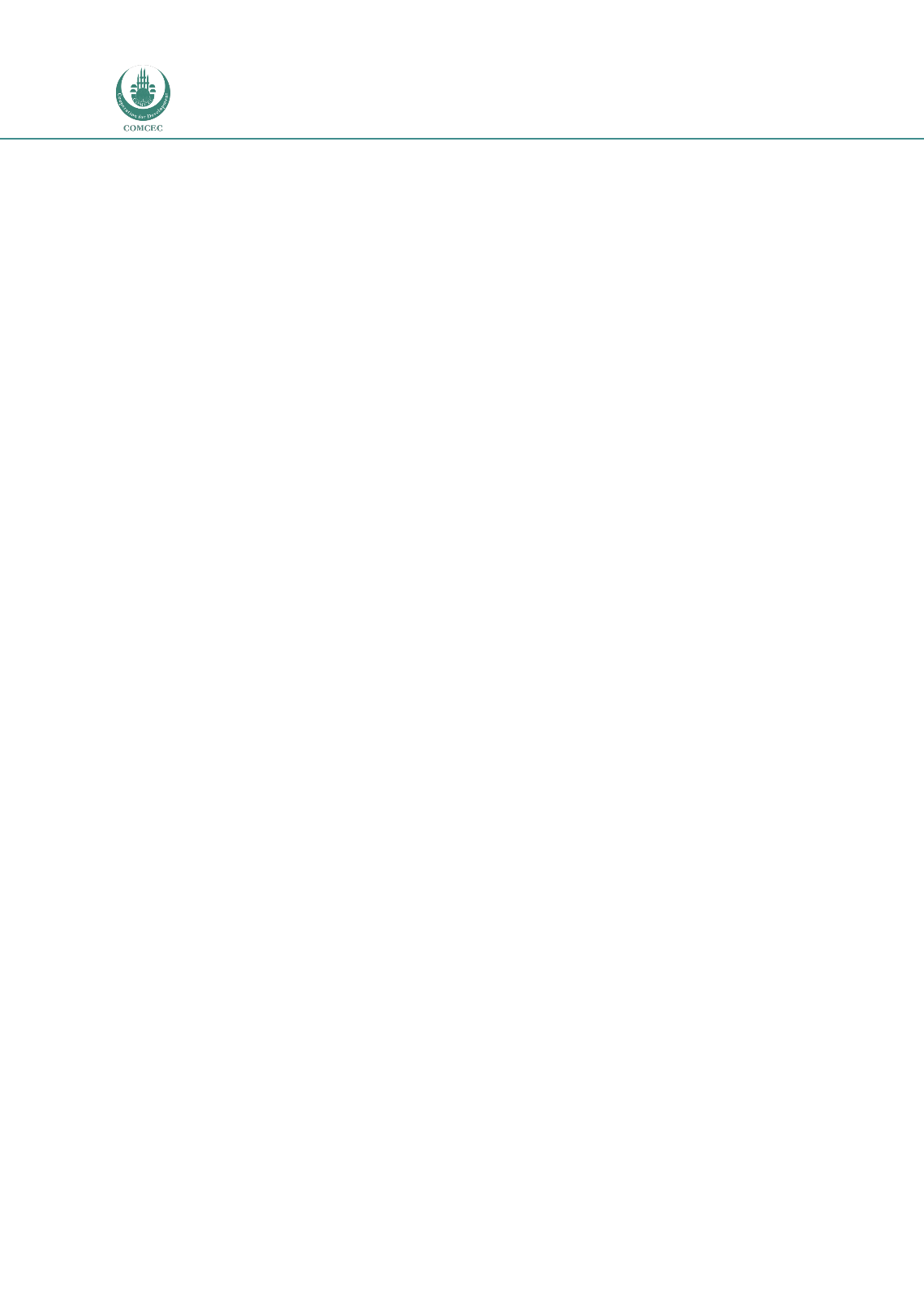
Promoting Agricultural Value Chains:
In the OIC Member Countries
108
5.6.3
Infrastructure and logistics
Since 1999, the textile industry has invested a total of approximately US$ 6.8 billion in
improving its infrastructure and modernising its mills and factories (USDA, 2014d).
The break-up of total investments indicates that 50.2 percent of investment was directed in the
spinning sector, followed by 17 percent in textile processing, 15 percent in weaving whereas
the investment in other sectors, namely knitwear, made ups and synthetic textiles, were at
respective rates of 7 percent, 4.7 percent and 5.8 percent (UNCTAD & Commonwealth Office,
2011).
However, the industry still faces challenges in keeping up with its competitors, as it failed to
diversify and upgrade its production capabilities by using better materials and technologies in
the production value chain (USDA, 2013b). The Textile Policy 2014-2019 recognises the
decrease in investment in the cotton and textile sectors since 2007 and the resultant
production inefficiencies. “The overall technological configuration of the industry needs major
up-gradation for replacing that machinery which has become obsolete or has outlived its
economic life” (Government of Pakistan, 2015). The Policy identifies a need for additional
investments of US$ 5 billion in machinery and technology for both basic and value-added
activities.
The lack of a reliable electricity supply due to frequent power outages is a further problem
facing the cotton and textile industry. Load shedding and power cuts are particularly
detrimental during the harvest period, as cotton cannot be processed and prices decrease
rapidly (Ghulam, 2014). This contributes to rising costs of production and processing, together
with increasing costs for inputs such as water, fertiliser and pesticides. Another constraint is
the limited availability of water for irrigation during peak sowing season from April to June,
particularly in the province of Sindh. Since much irrigation infrastructure is operated through
electricity, frequent power cuts add to water shortages for cotton production (USDA, 2012b).
The textile industry has therefore invested in its own energy infrastructure for mills to meet
export demands (USDA, 2014d).
5.6.4
Governance and value chain actors
The cotton value chain consists of input suppliers, cotton producers, middlemen and ginning
factories that separate the cotton fibres from the seed and thus turn seed cotton into cotton
lint (se
e Figure 5-19). In the subsequent textile value chain, the cotton is processed into cotton
yarn by spinning factories, sold to the textile industry which weaves it into fabric and finally
the garment industry produces textile items, such as clothing. Output at each stage of the value
chain can be exported.